ハンディーターミナル による、物流倉庫業務の改善事例
ハンディーターミナル +『たんと』=出庫検品システム
大阪プラント株式会社 様
トナーカートリッジ再生技術のパイオニア企業の大阪プラント株式会社は、最新機種の開発、部品調達、商品解析で常に業界を先駆しています。
導入前の問題点
ミスをなくす・作業効率を高めるシステムが急務
大阪プラント株式会社では、商品管理が電子化されておらず、当然の事ながら入出荷作業は人の目によって数えるため、出荷ミスが1か月に数回も発生していました。
同社では、そんなミスがおこるたびに緊急の出荷対応をせまられ、代替品の出荷作業が発生する等、現場での作業時間が延長され、事務所処理においても緊急出荷の伝票処理、その後の返品処理など、ミスから発生する対応に多くの時間を割かなければならなりませんでした。
また、顧客からの要望の多い、当日発注・当日出荷の締め切り時間延長にも応えるために、できるだけムダを省き、作業効率を高めるべくシステムの導入が必要でありました。
弊社の提案
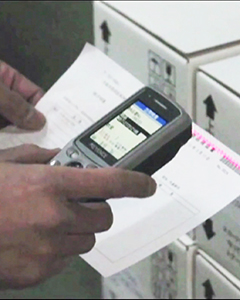
ハンディーターミナルを使用した出庫検品システムの導入を実施。
現場へのフィッティングにより、より現場目線のものにカスタマイズ化。
初めてのハンディーターミナル使用となるため1か月の試行期間を設置
最終の運用形態に近いプロトタイプを導入し、さらなる問題点を追求
現場での操作性を重視し、複雑な操作をできる限り排除するように努めました。
徹底した手入力の排除を実施。誤出荷の可能性を潰して行きます。
導入効果/お客様の声
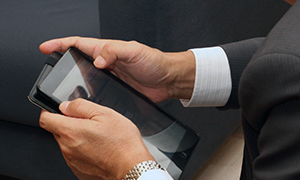
★導入から1年半経過するが、誤出荷が完全になくなった。
★当日受注・当日出荷の締切時間は当初の目標より1時間遅く16:00に延長できた。また出荷業務も当初と同じ時間で終了できた。
★ハンディーターミナルで、送り状No.をスキャンする事でお客様へメールで送り状No.を連絡する事が可能となった。
お客様の声
システム導入後、出荷ミスがなくなった事で、作業時間も大幅に短縮できたのはもちろんの事、顧客に対する会社の信頼度も向上した事は予想外の効果でした。
検品データは現場で収集、集めた情報はサーバーで一元管理。ハンディターミナルと「たんと」の連携で現場を見える化します。見える化は作業のミスを減らしスピードを上げます。
システム開発事業
○パッケージ開発
○クラウド開発
○基幹システム連携開発
- IBM i(AS/400)販売・保守・開発
- 基幹システム連携開発
- 購買・在庫管理システムの導入事例
- 汎用ソフト連携システム開発
- 物流・倉庫業のハンディーターミナルを使用した各種業務システム導入
- ハンディーターミナル活用事例
○CSV
システムコンサルティング
○物流業務改善
○クラウド活用提案
○EDIソリューション
リテール事業
○御社のPC係になります
- パソコンレスキュー隊「緊急PCヘルパー」
○御社の電話係になります
○リモートワーク
- 社外から社内ネットへの接続 テレワーク環境構築
- WEBコミュニケーション環境 WEB会議システム構築
○HP制作、教室
- ホームページ開発・運用・アドバイス・活性化・SEO支援・ECサイト構築支援
- 社内で改造!HP改造教室付きホームページ作成 10万円~